A Comprehensive Guide to Welding Evaluation: Comprehending Specifications, Techniques, and Ideal Practices for Top Quality Guarantee
Welding examination plays a pivotal role in guaranteeing the structural integrity and safety of welded components, demanding an extensive understanding of market standards such as those established by AWS and ASME. Various evaluation techniques, consisting of aesthetic and ultrasonic testing, are employed to spot potential defects that might compromise high quality. Applying finest practices can significantly improve operational reliability and foster trust fund amongst clients. As we discover these essential aspects, it becomes noticeable that the effects of welding inspection expand far beyond conformity, inviting a more detailed evaluation of how these procedures form industry criteria and techniques.
Significance of Welding Inspection
Welding evaluation plays a crucial function in making sure the honesty and safety of bonded structures. It is an essential process that confirms that welds satisfy predefined specs, which is vital in various sectors, including building, vehicle, and aerospace. By conducting detailed evaluations, prospective problems such as cracks, insufficient fusion, and porosity can be determined early, stopping tragic failings that can lead to accidents or costly repair services.
The importance of welding inspection extends beyond mere compliance with regulations; it also fosters trust with stakeholders. Clients and governing bodies anticipate guarantee that the frameworks they rely upon are developed to endure operational tensions. Additionally, effective welding inspection methods add to long-lasting toughness and efficiency of the structures, ultimately leading to reduced maintenance prices.
In addition, welding inspection advertises a society of high quality within companies, urging adherence to finest practices and continual enhancement. By integrating inspection processes right into the welding process, companies can boost their credibility and develop themselves as leaders in quality control. To conclude, the relevance of welding inspection exists in its capability to guard lives, make sure structural dependability, and support sector standards, making it an essential facet of welding operations.
Key Sector Specifications
Ensuring compliance with vital market criteria is important for keeping the quality and safety of bonded structures. Different companies establish these requirements to advertise best methods in welding and inspection - Welding Inspection Gilbert Arizona. Among one of the most acknowledged are the American Welding Culture (AWS) and the American Society of Mechanical Engineers (ASME), which give detailed standards and requirements for welding processes and evaluation requirements
AWS criteria, such as AWS D1.1 for structural welding, synopsis requirements for materials, style, and screening to ensure the integrity of welds. Likewise, ASME codes, consisting of ASME Area IX, control the certification of welders and welding treatments, ensuring constant high quality in commercial applications. Worldwide, the ISO 3834 typical emphasizes quality requirements for fusion welding, providing a framework for organizations to show conformity with international ideal techniques.
Conformity with these criteria not just improves the dependability of welded structures but additionally minimizes threats linked with architectural failures. Adherence to market standards is frequently a prerequisite for governing authorizations and can substantially influence job specs. Ultimately, understanding and implementing these vital requirements are vital for effective welding inspection and top quality assurance.
Inspection Techniques Review
Effective welding inspection counts on a variety of strategies created to evaluate the top quality and integrity of welds. These strategies can be extensively classified right into non-destructive and devastating testing (NDT) methods. Non-destructive testing techniques, which are widely chosen in the sector, enable the analysis of welds without find jeopardizing the integrity of the product.
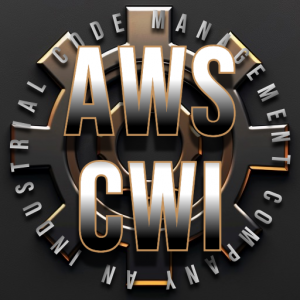
Among the most typically utilized NDT methods are visual assessment, ultrasonic screening, radiographic screening, and magnetic particle testing. Visual inspection is frequently the very first step in the assessment process, enabling inspectors to identify surface flaws and examine weld bead accounts.
Each strategy has its own benefits and constraints, making it crucial for assessors to pick the most suitable method based on the specific needs of the task, the products included, and the criticality of the welds being inspected. This mindful choice makes sure thorough analyses and maintains safety and security and high quality standards in welding procedures.
Usual Flaws and Their Ramifications
A complete understanding of typical defects in welds is crucial for keeping structural honesty and security in welded building and constructions. Welding issues can dramatically jeopardize the mechanical residential properties of the joint, resulting in failings that might jeopardize both workers and equipment.
Typical defects consist of porosity, which materializes as small gas pockets entraped in the weld metal, deteriorating the overall framework. Cracking is an additional prevalent problem, often arising from rapid air conditioning or improper joint layout, bring about anxiety concentrations that can result in devastating failures. Insufficient fusion occurs when the weld steel fails to appropriately bond with the base product, creating powerlessness that might result in splitting up under lots.
Various other noteworthy flaws consist of undercutting, where the weld bead wears down the base steel, and slag inclusions, which can hinder the weld's stamina. Each of these issues has specific implications; for example, porosity can lower ductility, while cracking directly impacts tensile stamina. Recognizing and recognizing these defects during evaluation is necessary for making certain and implementing corrective measures compliance with industry standards, ultimately safeguarding the structural integrity of welded assemblies.
Best Practices for Quality Guarantee
Applying ideal techniques for top quality guarantee in welding procedures is vital for accomplishing ideal results and reducing problems. One crucial practice is the facility of clear welding treatments that stick to industry standards and specifications. These treatments must consist of in-depth directions regarding product option, joint preparation, and welding techniques to ensure uniformity and high quality.
Routine training Website and accreditation of welding personnel are likewise essential. Competent welders who understand the significance of quality control are most likely to generate sound welds. Additionally, implementing a durable evaluation program, consisting of both aesthetic and non-destructive screening (NDT), can help determine issues early in the procedure, allowing why not look here for prompt corrective activities.
Lastly, promoting a culture of quality within the company encourages employees to prioritize quality in their work. By sticking to these best practices, organizations can boost the honesty of their welding processes, inevitably leading to improved product high quality and minimized prices connected with rework and repairs.
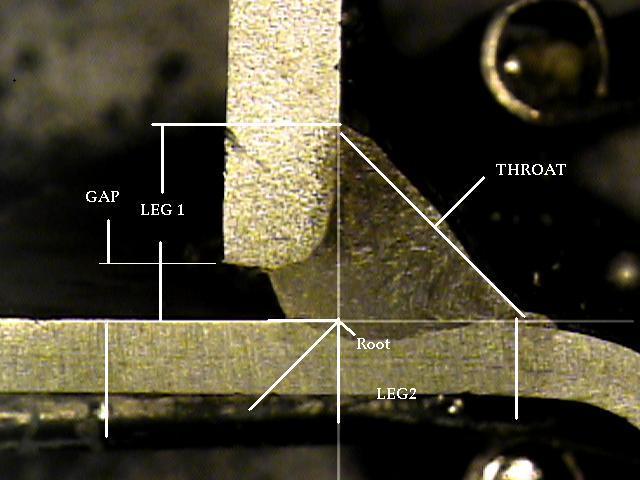
Final Thought
In conclusion, welding assessment plays an important duty in making sure the honesty and security of welded frameworks. By carrying out best techniques, companies can enhance integrity, lessen maintenance expenses, and cultivate trust fund amongst clients, inevitably contributing to effective welding operations.
Additionally, welding examination promotes a society of top quality within organizations, urging adherence to finest techniques and continuous renovation. In conclusion, the relevance of welding inspection lies in its capacity to safeguard lives, make sure architectural reliability, and maintain sector standards, making it a crucial aspect of welding procedures.
Amongst the most recognized are the American Welding Society (AWS) and the American Culture of Mechanical Designers (ASME), which provide in-depth standards and requirements for welding processes and evaluation requirements.
Inevitably, understanding and implementing these essential requirements are crucial for effective welding evaluation and high quality guarantee.
Reliable welding examination relies on a variety of techniques developed to evaluate the quality and integrity of welds.